VOLGEND ARTIKEL
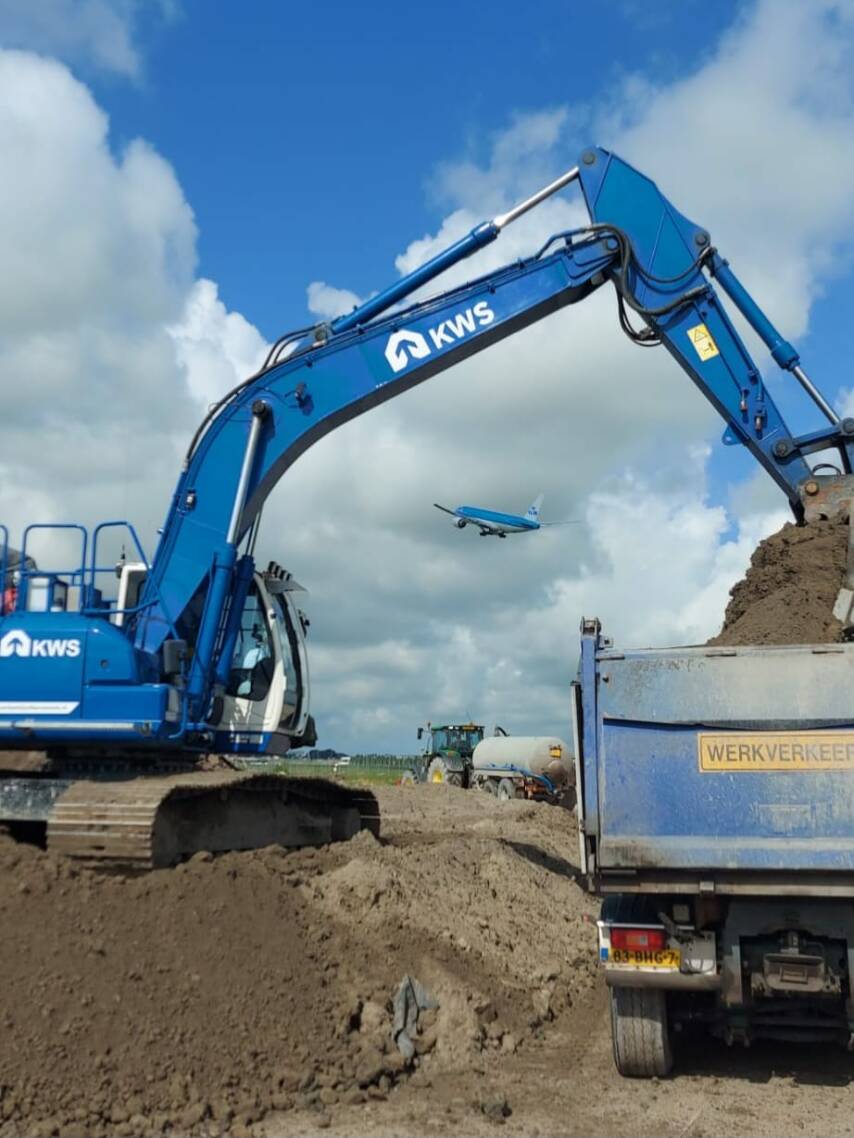
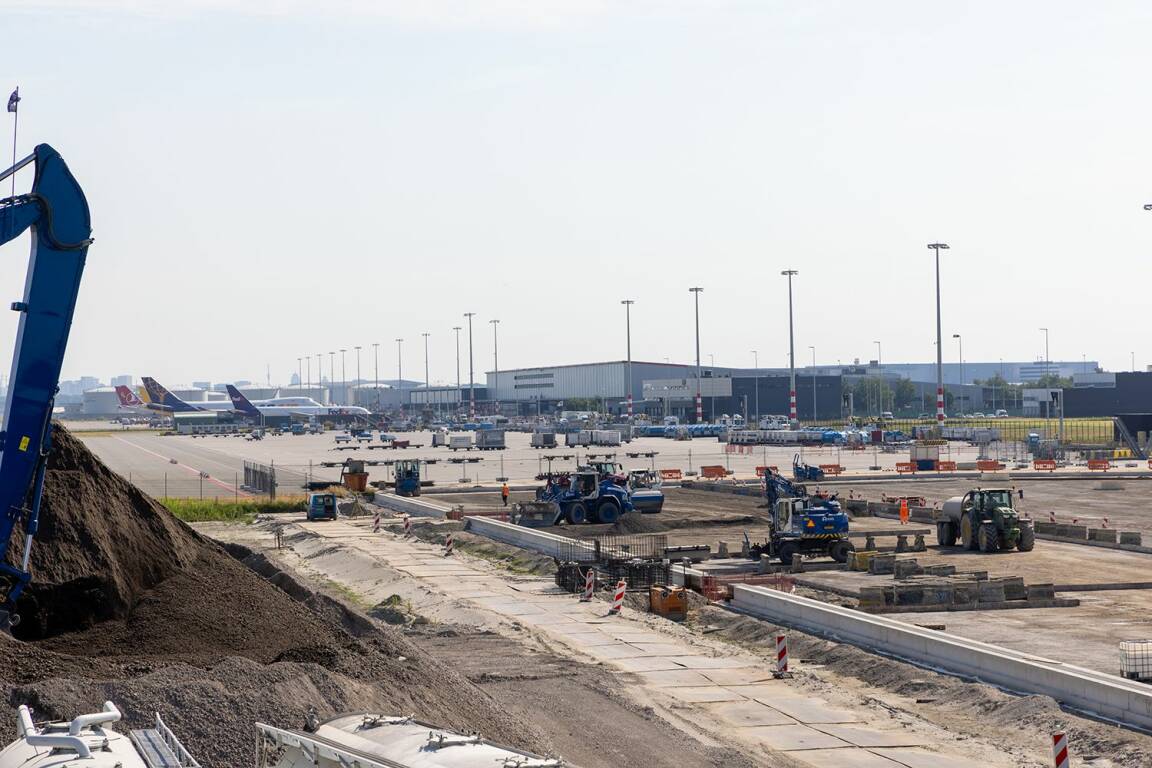
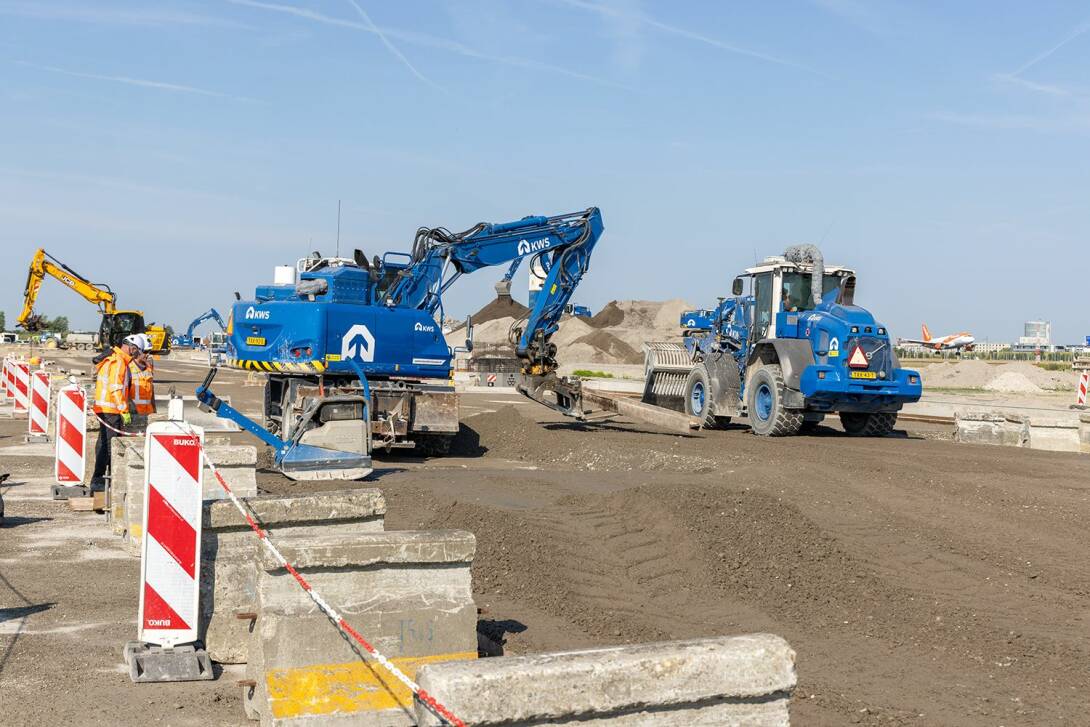
‘WE MAKEN HIER EEN MOOI WERK MET Z’N ALLEN’
Dennis kijkt uit naar het vervolg van de samenwerking: ‘We hebben samen een duidelijk doel: dit project tot een goed einde brengen en een goede oplossing voor Schiphol realiseren. Dat werpt zijn vruchten af, want we maken hier mooi werk met z’n allen in een fijne sfeer van wederzijds vertrouwen.’
3D-BESTUURDE KOLOS
Van de betonpaver die gebruikt wordt bij het project zijn er slechts twee in Nederland te vinden: de Wirtgen SP1600 van BKB Infra, onderdeel van KWS. Het is het grootste exemplaar van zijn soort en op het Sierra-platform te bewonderen. Deze kolos van zo’n zestien meter lang, legt de betonverharding aan in stroken van tien meter breed. Dit gebeurt volledig zelfstandig met behulp van een 3D-machinebesturing. Het resultaat is een prachtig vlak geheel. Voor de productie van de betonmortel staat de mobiele betoncentrale van MCG op zo’n zeven kilometer van het werk. Hierdoor is de transportafstand kort en kunnen we snel bijsturen om de kwaliteit hoog te houden.
DUURZAAM BOUWEN
KWS legt het nieuwe platform zo duurzaam mogelijk aan. De werkvoertuigen rijden op HVO100-brandstof, een duurzaam en nagenoeg CO2-neutraal alternatief voor diesel. Om het gebruik van grondstof te verminderen, wordt het betonplatform op een bepaald gedeelte minder dik. Ook wordt er een cementloze CERO-elementverharding (met geopolymeer in plaats van cement) toegepast.
Vrachtvliegtuigen vanuit de hele wereld leveren hier hun lading af: het Sierra platform aan de westkant van de luchthaven. Een indrukwekkende plek van 280 meter lang en 80 meter breed, vergelijkbaar met de oppervlakte van bijna drie voetbalvelden. Ruimte genoeg voor KWS om hier drie nieuwe opstelplekken te verwezenlijken voor de vrachtvliegtuigen.
Dankzij de ruime opstelplaatsen kan de vracht gemakkelijk tussen vliegtuig en loods verplaatst worden. Het project is een mooi visitekaartje voor KWS. Dennis de Haan – sinds een jaar projectleider van KWS – is erg enthousiast over de samenwerking: ‘Welke uitdaging we ook tegenkomen in het project Sierra 3, Schiphol beschouwt het als onze gezamenlijke uitdaging. Ze zeggen niet: ‘aannemer, het is jouw probleem, los het maar op.’
Honderdduizenden vliegbewegingen, miljoenen passagiers en ruim een miljoen ton goederen. Op het dynamische Schiphol bruist het van de activiteit. Maar ook áchter de schermen wordt hard gewerkt om de luchthaven draaiende te houden. VolkerWessels Infra Schiphol – bestaande uit KWS en Vialis – realiseert er bijvoorbeeld opstelplekken voor de grootste vrachtvliegtuigen.
DUURZAAM WERKEN NEEMT VLUCHT OP SCHIPHOL
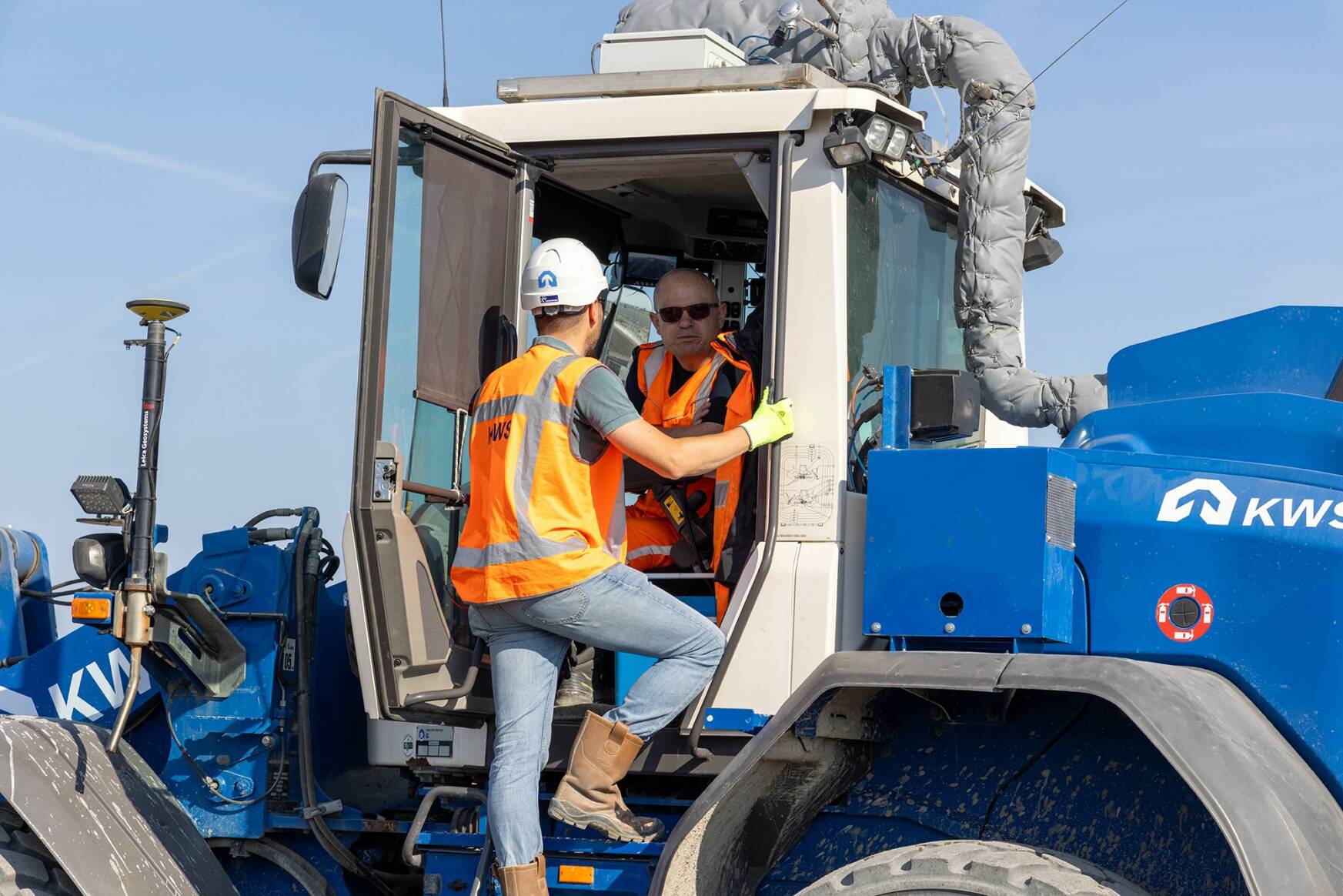
VOLGEND ARTIKEL
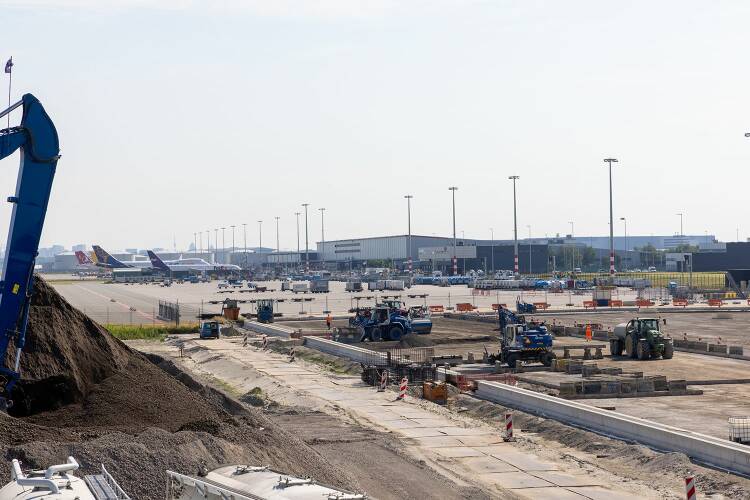
‘WE MAKEN HIER EEN MOOI WERK MET Z’N ALLEN’
Dennis kijkt uit naar het vervolg van de samenwerking: ‘We hebben samen een duidelijk doel: dit project tot een goed einde brengen en een goede oplossing voor Schiphol realiseren. Dat werpt zijn vruchten af, want we maken hier mooi werk met z’n allen in een fijne sfeer van wederzijds vertrouwen.’
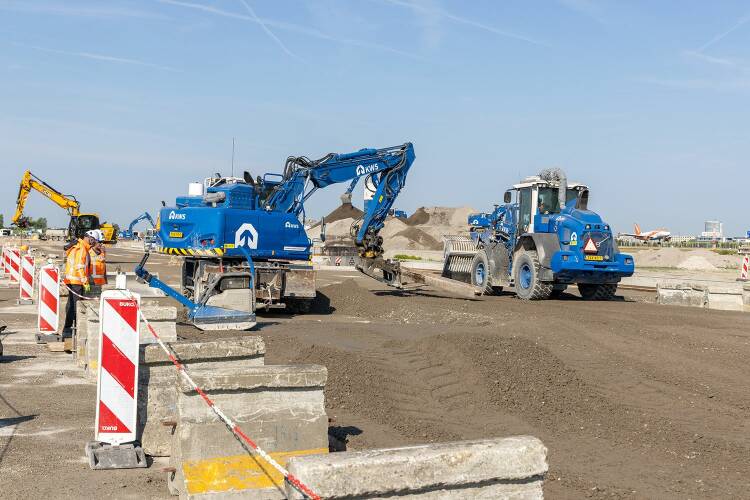
3D-BESTUURDE KOLOS
Van de betonpaver die gebruikt wordt bij het project zijn er slechts twee in Nederland te vinden: de Wirtgen SP1600 van BKB Infra, onderdeel van KWS. Het is het grootste exemplaar van zijn soort en op het Sierra-platform te bewonderen. Deze kolos van zo’n zestien meter lang, legt de betonverharding aan in stroken van tien meter breed. Dit gebeurt volledig zelfstandig met behulp van een 3D-machinebesturing. Het resultaat is een prachtig vlak geheel. Voor de productie van de betonmortel staat de mobiele betoncentrale van MCG op zo’n zeven kilometer van het werk. Hierdoor is de transportafstand kort en kunnen we snel bijsturen om de kwaliteit hoog te houden.
DUURZAAM BOUWEN
KWS legt het nieuwe platform zo duurzaam mogelijk aan. De werkvoertuigen rijden op HVO100-brandstof, een duurzaam en nagenoeg CO2-neutraal alternatief voor diesel. Om het gebruik van grondstof te verminderen, wordt het betonplatform op een bepaald gedeelte minder dik. Ook wordt er een cementloze CERO-elementverharding (met geopolymeer in plaats van cement) toegepast.
Vrachtvliegtuigen vanuit de hele wereld leveren hier hun lading af: het Sierra platform aan de westkant van de luchthaven. Een indrukwekkende plek van 280 meter lang en 80 meter breed, vergelijkbaar met de oppervlakte van bijna drie voetbalvelden. Ruimte genoeg voor KWS om hier drie nieuwe opstelplekken te verwezenlijken voor de vrachtvliegtuigen.
Dankzij de ruime opstelplaatsen kan de vracht gemakkelijk tussen vliegtuig en loods verplaatst worden. Het project is een mooi visitekaartje voor KWS. Dennis de Haan – sinds een jaar projectleider van KWS – is erg enthousiast over de samenwerking: ‘Welke uitdaging we ook tegenkomen in het project Sierra 3, Schiphol beschouwt het als onze gezamenlijke uitdaging. Ze zeggen niet: ‘aannemer, het is jouw probleem, los het maar op.’
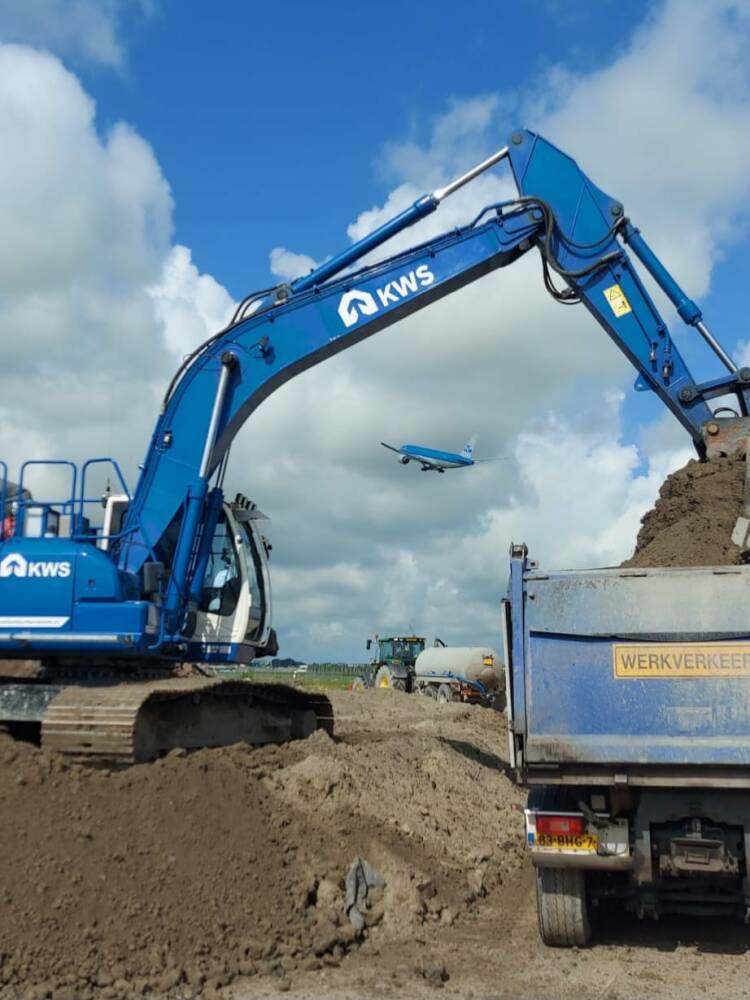
Honderdduizenden vliegbewegingen, miljoenen passagiers en ruim een miljoen ton goederen. Op het dynamische Schiphol bruist het van de activiteit. Maar ook áchter de schermen wordt hard gewerkt om de luchthaven draaiende te houden. VolkerWessels Infra Schiphol – bestaande uit KWS en Vialis – realiseert er bijvoorbeeld opstelplekken voor de grootste vrachtvliegtuigen.
DUURZAAM WERKEN NEEMT VLUCHT OP SCHIPHOL
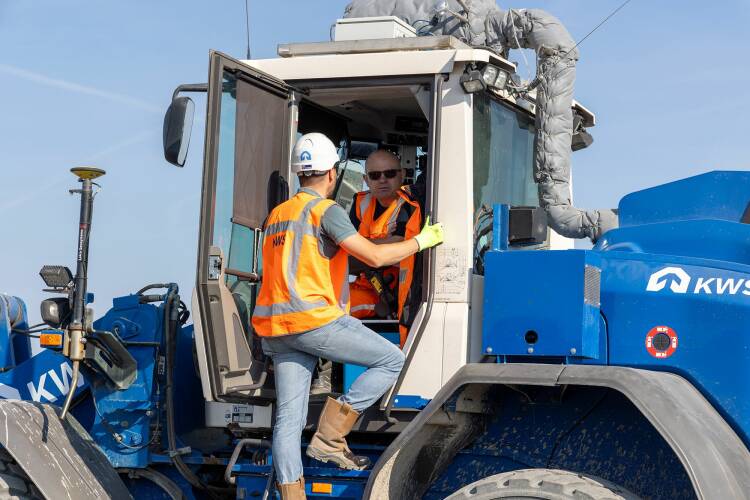